|
 |
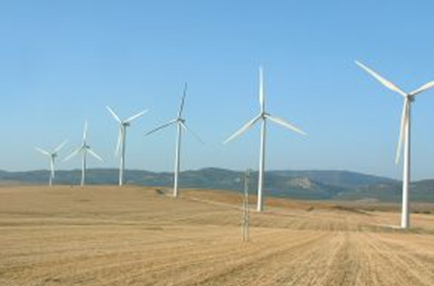
The glass is very hydrophilic and attracts water to the interface which could lead to bond weakness between glass fibre and resin. Silane is a critical component of glassfibre-reinforced polymers could improve bond property between glass fibre and resin. Silane coupling agent significantly increased strength, electrical property, water-resistant and weather resistance property of glassfibre-resinforced polymers. Even in wet status, silane coupling agents could also significantly improved mechanical property of polymers. Silane coupling agents are used on glass fibre for general purpose which covers 60% of total consumption. As per the different chemical structure of film forming resin, the general application silane coupling agent in glass fibre are epoxy silane, amine silane and methacryloyl silane e.g. SCA-403, SCA-1113, SCA-503.
Glass fibre treating agent includes film-forming agent, anstatic agent, surfactant, coupling agent water. Coupling agent covers 0.3%-2% of total glass fibre surfactant. Acidified water with organic acid to a certain PH value ( amine silane is more alkalized after hydrolyzation without PH adjustment.), stir fully and add certain silane until transparent, then add other components. For some insoluble silanes could add some additives such as ethanol and isopropanol. The stability of silane solutions depend on coupling agents type and concentration, the hydrolization occurs in the process of solution configuration, the latter silicon hydroxyl would auto condensation form Silicon silicon and oxygen chemical bond so the configuration solution should be used promptly.
|
Filler has become increasingly important additives and modifiers for organic polymer which plays an important on cost down and improving product performance. The hydroxyl on filler surface is usually hydrophilic and incompatible with organic polymers. Alkoxysilane is used to treat mineral surface, the hydroxyl on mineral surface condenses with hydroxyl generated in silane hydrolization, the organic side on silane is outward to make it more compatible and dispersible which could improve coupling of resin and filler or even transfer the filler to a strengthen additives. Silane treatment could improve product processing property, mechanical property and durability as followings:
1. Increased bond between filler and polymer
2. Improved impregnation performance to polymer
3. Promoted dispersity in polymer
4. Improved mechanical property
5. Reduced viscosity of filler or polymer mix
The choice of silane to be used determined by the nature of desired benefit. All the alkoxysilanes will bond to filler or mineral surface easily. The PH value of filler surface and moisture could catalyse silane hydrolysis fully so there is no need for extra hydrolysis in the process of filler treating.
The following rules should be followed in the process of filler surface modification:
◇ If the silane treatment is designed to provide surface hydrophobicity, so a silane with hydrophobic group such as methyl, decyl, octyl, dodecyl , hexadecyl or phenylshould be chosen. Such as SCA-103、SCA-203H、SCA-213D,SCA-203E,SCA-203F,SCA-1303.
◇ If the silane treatment is designed to offer compatibility between polymer and filler so the nature of organic group on silane should be similar to chemical structure of polymer, such as SCA-203D, SCA-203E, SCA-203F are recommended to be used in polyolefin matrix.
◇ If the silane treatment is bond a filler to a polymer matrix so a organo-reacitve silane should be chosen such as SCA-8503, SCA-503, SCA-403, SCA-1113.SCA-603 and SCA-1603.
|
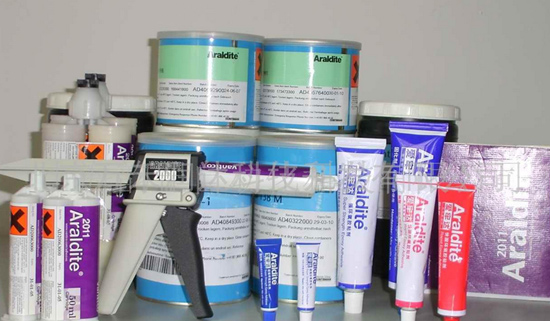
Inorganic filler are widely add into adhesives to improve organic adhesive properties ( dry-wet adhesion, mechanical property, storage stability, heat resistance, moisture resistance, and weatherability) or reduce adhesive cost. If the filler is pre-treated by silane, the structural effect between filler and resin could be greatly reduced, also could greatly improved compatibility and dispersity on adhesive matrix resin and significantly reduced viscosity, so the filler consumption increased. The silane treatment effects on filler depends on filler varieties, greatly effective on filler with large amount of hydroxyl such as glass, silica and alumina, failed on filler without hydroxyl on surface e.g.calcium carbonate and graphite. Widely used silanes in adhesive are SCA-1113、SC-603、SCA-503、SCA-403、SCA-1603、SCA-1103E、SCA-3303 etc.
|
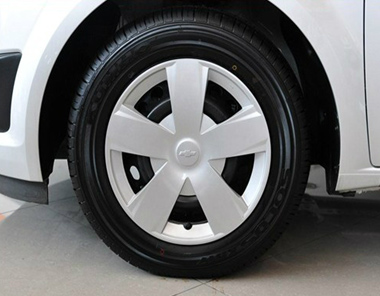
The special properties of silanes are used to enhance performance and improve processes in rubber and plastics industries. Silanes could be used as coupling and dispersing agents for fillers in plastics and rubber, as polymerization modifier in the synthesis of polypropylene to enhance isotacticity and as crosslink agents in polyethylene homopolymers and copolymers to increase crosslingking points.
1. Rubber Compounding
Silane is widely used in organic rubber industry due to benefit of replacing carbon black by inorganic filler for reinforcement rubber. Compared with black carbon, carbon white and other inorganic filler reinforcement for rubber could offer unique physical and mechanical properties, silanes are necessary for non-black reinforcement fillers to be effective.Silane application is a key factor for effective bond between inorganic filler and Organic elastomer. Silane-coupled and mineral filled rubber products are used for Automotive, offroad tyres, shoe soles, belts, flexible pipe and other mechanical products, widely used silanes in rubber are SCA-903、SCA-1113、SCA-403、SCA-1603.
2. Plastic compounding
Application for manufacturing cross-linked polytene, cable insulation and Sheath material: In an extruder in the presence of peroxide and heat, the vinyl group will graft to the polyethylene backbone, yielding a silane-modified polyethylene that contains pendant trialkoxysilyl functionality. The grafted polyethylene can then be immediately crosslinked in the presence of a tin catalyst, moisture and heat to create a silane-cross-linked product. Widely used silanes in plastic compounding are SCA-1603,SCA-1613,SCA-1623.
Silane-crosslinked polyethylene is used for electrical wire and cable insulation and jacketing where ease of processing, increased temperature –resistance, abrasion resistance, stress-crack resistance, improved low temperature properties and retention of electrical properties are needed. Application for cold and hot water pipe where resistance to long-term pressure at elevated temperatures, natural gas pipe with good resistance to stress cracking, foam for insulation and packaging with greater resiliency and heat resistance.
|
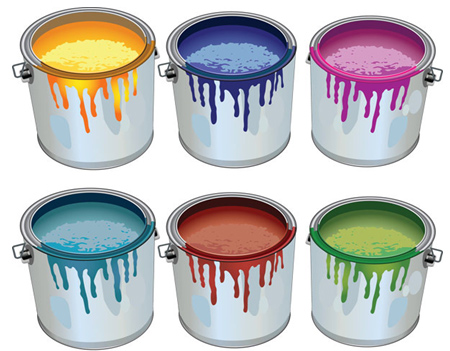
Silane modification became a key technology in high performance painting due to unique ability to form covalent bond between inorganic and organic compounding and inner stability of silicon oxygen bonding, silanes provide anti physics, chemical, environment and heat-degration propertities.
Silane monomer as organic functional alkoxysilane could be widely used in painting as adhesion promoter, painting treating agent and cross-link agent. Inorganic alkoxysilane could bond with varieties of organic functional groups to form covalent bond between organic polymers and inorganic surface ( such as dye, filler, glass and metal materials). All alkoxysilanes bond with inorganic filler surface are the same in nature, To optimize silane performance, the chemical nature of silane reactive functional group and hydrolyzable alkoxy functional group should be matched with organic polymer of painting or ink.
Widely used silanes in painting and ink are SCA-503、SCA-1603、SCA-403、SCA-1113、SCA-4603、SCA-1103B、SCA-1103E
Silane will endue painting many strongpoint ,include:
1. Promoted coating adhesion
2. Promoted coating durability
3. Promoted coating weatherability
4. Promoted coating toughness
5. Significantly reduced dispersion viscosity of filler and painting
6. Promoted painting dispersity
|
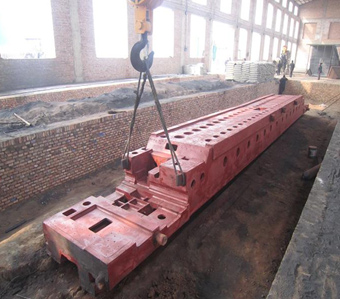
In the process of casting, should use natural synthetic resin as model and core sand adhesion, due to structure and nature difference it is hard to form chemical bond and could not mutual penetration and dissolution, so generally silane is adopted to enhance adhesion. Adding silane could not only improve resin sand strength and also could reduce total quantity of resin and weakness of Casting porosity type, promote thermal stability and elevated temperature property that could effectively enhance casting quality and cost down. Widely used silanes in casting are SCA-602、SCA-1113、SCA-2013、SCA-403. If do not concern too much about strength some amine silane high boiling residues are widely application due to low cost.
|
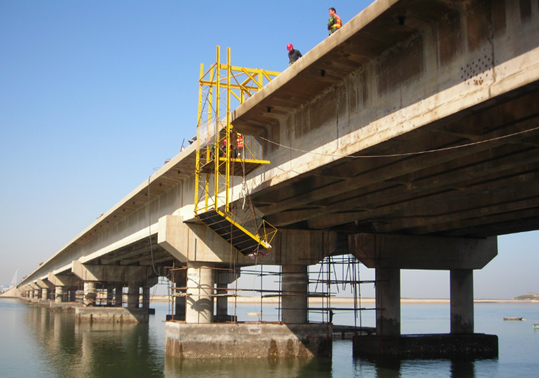
Concrete structural durability deterioration led to extremely reduction on structural reliability and safety which harm to structural regular service. The steel bar corrosion is main reason for durability reduction which cause huge economic loss. Silane surface Hydrophobic treatment could reduce concrete corrosion probability and rate caused by outside chlorid ion penetration, postpone corrosion period and reduce corrosion steel mass loss rate.
Silane impregnation could significantly improved concrete structural durability with advanced technology, convenient operation, safety and durability, economic and environmental friendly natures has approved by national authorities.
The strong hydrophobicity of octyl could transform hydrophilic concrete surface and pore wall into hydrophobicity which could effectively.stop the penetration of harmful materials.
Fairly use Silane impregnation technology could obtain properties as below:
1. Excellent water repellent performance could reduce concrete structure water absorption to more than 90%.
2. A water repellent material with breath function.
3. Application for construction with special requirements on appearance without changing.
4. Excellent alkali resistance and durability reduce repair frequency and cost.
5. Effectively keep good appearance of concrete structure for a long term.
|
|
|
|
|